Firmy produkujące okna, drzwi i rolety muszą zapewniać nie tylko wysoką jakość wytwarzanych produktów, ale także optymalizować procesy, ograniczać koszty i wprowadzać rozwiązania ekologiczne. Moduł „Zarządzanie produkcją” wspiera producentów w cyfrowej transformacji procesów wytwórczych. Jest to kompleksowe rozwiązanie o szerokich zaletach:
Moduł "Zarządzanie produkcją"

- Moduły
- Zarządzanie produkcją
Nowoczesne zarządzanie produkcją okien, drzwi i rolet
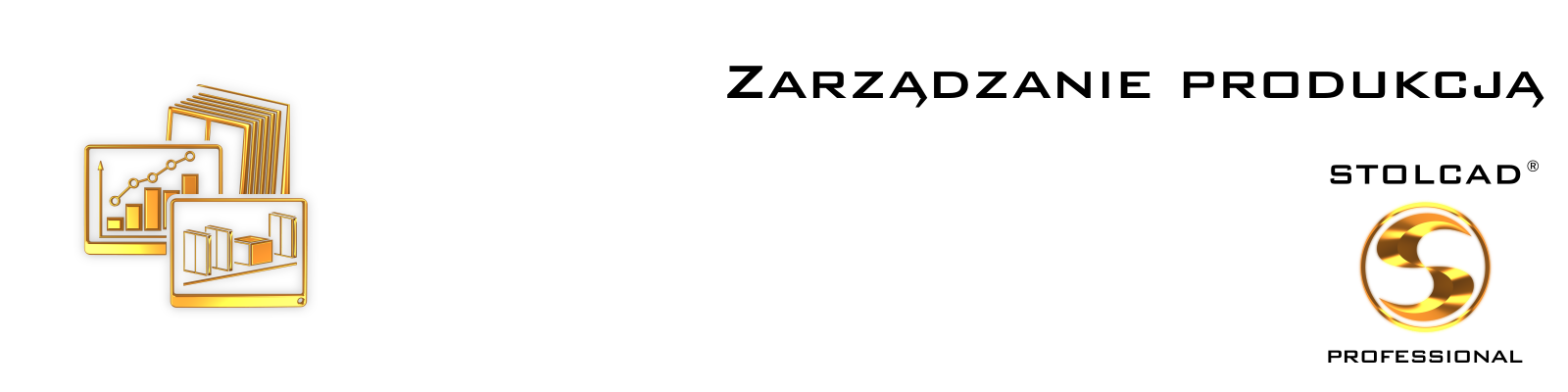
Zarządzanie i nadzór nad procesami produkcyjnymi okien, drzwi i rolet
- Zdalna kontrola procesu produkcyjnego
- Redukcja kosztów produkcji i lepsze wykorzystanie zasobów
- Oszczędność czasu ‒ krótszy czas produkcji
- Ekologiczna produkcja „bezpapierowa”
- Przewidywalność procesu produkcji
- Usprawnienie przepływu informacji
- Wyższa produktywność kadry pracowniczej
- Szybkie identyfikowanie i rozwiązywanie problemów na produkcji
Moduł „Zarządzanie produkcją” składa się z trzech zintegrowanych rozwiązań IT:
Aby korzystać z możliwości modułu „Zarządzanie produkcją” niezbędne jest wdrożenie modułu „Etykieta produkcyjna”. System wykorzystuje technologię skanowania kodów kreskowych z etykiet, co umożliwia efektywne śledzenie i kontrolę procesów produkcyjnych.
Moduł "Podgląd na produkcji"
Wyświetlanie list montażowych dopasowanych do poszczególnych etapów produkcji
Moduł „Podgląd na produkcji” to narzędzie umożliwiające usprawnienie procesów wytwórczych. Korzysta z kodów kreskowych umieszczonych na etykietach produkcyjnych, naklejanych na profile. Etykiety te są generowane automatycznie przez program Stolcad® Professional. Mogą być drukowane na piłach lub centrach tnących wyposażonych w drukarki, na podstawie danych dostarczonych przez Stolcad® Professional. Jeżeli maszyny te nie mają drukarek, etykiety można wydrukować w biurze.
Wtedy są one drukowane w takiej samej kolejności, jaka wynika z optymalizacji cięcia profili. Pracownik nie musi szukać konkretnych etykiet, ponieważ kolejne cięcie zawsze odpowiada kolejnej etykiecie. Alternatywą dla kodów kreskowych na etykietach jest programowanie elektronicznego zapisu danych w chipach i umieszczanie ich na profilach. Takie rozwiązanie stosuje się w przypadkach, gdy użycie klasycznych etykiet jest kłopotliwe, np. w technologiach drewnianych.
Na poszczególnych stanowiskach pracy umieszczone są komputery ze skanerami kodów kreskowych lub alternatywnie chipów. Na kolejnych etapach produkcji dane zawarte w kodzie kreskowym lub chipie umożliwiają szybką identyfikację poszczególnych elementów. Dzięki nim można rozpoznać, z którego zlecenia i pozycji pochodzą. Rozróżniane są także poszczególne części konstrukcji, takie jak rama czy skrzydło.
Pracownik, skanując kod na swoim stanowisku roboczym, otrzymuje z bazy danych komplet informacji produkcyjnych dotyczących tych elementów, które są niezbędne do dalszej pracy na jego stanowisku. Na ekranie komputera wyświetlają się elementy potrzebne do zamocowania, wybrane dla tego stanowiska, oraz rysunek dostosowany do jego potrzeb.
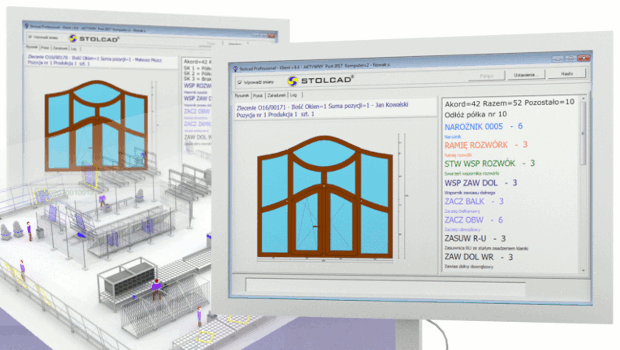
Historie z hali produkcyjnej – lepsza organizacja, szybsza produkcja
Wyobraźmy sobie typowy dzień pracy na hali produkcyjnej. Pracownik podchodzi do swojego stanowiska, gdzie czeka na niego zadanie w ramach etapu produkcji okien, drzwi lub rolet. Wcześniej musiałby przeszukiwać dokumentację, aby dowiedzieć się, jakie elementy są niezbędne do realizacji zlecenia. Dzisiaj wystarczy jedno skanowanie kodu kreskowego umieszczonego na etykiecie produkcyjnej, aby na ekranie monitora pojawiła się dokładna lista elementów do wykonania. Pracownik od razu wie, co powinien zamontować i jak wygląda gotowy produkt. Nie traci czasu, nie popełnia błędów. Wszystko odbywa się płynnie i bez przestojów. Taki scenariusz to rzeczywistość dzięki modułowi „Podgląd na produkcji”.
Zredukowanie chaosu i automatyzacja kluczowych procesów nie tylko poprawiają efektywność, ale także zwiększają komfort pracy. Pracownicy mogą skupić się na swoich zadaniach zamiast tracić czas na poszukiwanie informacji. Moduł umożliwia definiowanie różnych rodzajów stanowisk roboczych, takich jak zbrojenie, zakładanie uszczelki, okuwanie, szklenie czy kontrola jakości. Moduł nie narzuca jakie są to stanowiska – technolog może dowolnie je określić. Dzięki temu rozwiązaniu pracownicy produkcyjni otrzymują tylko te dane, które są w danym momencie niezbędne. W efekcie oszczędza się czas, który bez modułu musiałby zostać poświęcony na manualną organizację dokumentacji i wyszukiwanie informacji dotyczących konkretnego stanowiska.
Skuteczna produkcja zaczyna się od indywidualnie dopasowanych list elementów
Pracownik skanując kod kreskowy zobaczy na swoim monitorze jakie elementy okna, drzwi lub rolety powinien zamontować na swoim stanowisku pracy, uwzględniając specyfikę wykonywanych zadań. Wyświetlane są listy potrzebnych elementów do realizacji konstrukcji – zawsze dostosowane do potrzeb danego stanowiska produkcyjnego. Elementy pokazywane na terminalach różnią się w zależności od stanowiska pracy na którym dokonano odczytu kodu kreskowego. Ta sama etykieta zeskanowana na dwóch różnych stanowiskach spowoduje wyświetlenie różnych informacji i rysunków.
Przykładowo na stanowisku szklenia pokazane będą szyby do zamontowania, a na stanowisku okuwania - okucia niezbędne do danego skrzydła. Również rysunek na stanowisku szklenia będzie zawierał wymiary szyb, a na stanowisku okuwania wymiary skrzydeł. O tym co ma być wyświetlane decyduje technolog podczas konfiguracji systemu. Taka personalizacja danych sprawia, że pracownicy szybko i efektywnie reagują na wymagania produkcyjne, ponieważ nie są zasypywani nadmiarem niepotrzebnych informacji.
Dzięki kolorystycznym oznaczeniom elementów niestandardowych i graficznym wizualizacjom gotowych produktów, nawet najmniejsze detale, które wymagają szczególnej uwagi, są natychmiast zauważane. Przykładowo na stanowisku okuwania skrzydeł można dane skonfigurować tak, aby elementy zmienne, takie jak zasuwnice, były wypisywane kolorem niebieskim, a nożyce kolorem zielonym. Dzięki temu pracownik szybko przyzwyczai się do tego, że informacja oznaczona kolorem niebieskim odnosi się do zasuwnicy, którą ma zamontować.
Rysunki konstrukcji mogą być indywidualnie skonfigurowane dla poszczególnych stanowisk. Jeśli konstrukcja zawiera więcej niż jedno skrzydło, program rozpozna i wyświetli informacje dotyczące wyłącznie zeskanowanego skrzydła, co jest szczególnie istotne na stanowisku okuwania. Taka wizualna pomoc zapewnia precyzyjne wykonanie każdego etapu produkcji, niezależnie od jego skomplikowania. Dzięki temu żaden kluczowy element nie zostanie pominięty. Pracownicy mogą błyskawicznie reagować na specyficzne wymagania, co podnosi jakość wyrobów i skraca czas realizacji zleceń.
Wyszczególnienie elementów krytycznych i nietypowych rozwiązań
Program Stolcad® Professional dopilnuje również, aby nietypowe i krytyczne elementy nie były nigdy pominięte. Wyszczególnienie elementów na ekranie produkcyjnym za pomocą kolorów pomaga pracownikom w ich identyfikacji. Elementy nietypowe mogą być zaznaczone jaskrawymi kolorami. Przykładowo standardowy narożnik lub zawias skrzydła może być wypisany kolorem czarnym. Natomiast jeżeli w danym skrzydle ma być zamocowany narożnik krótki lub zawias powyżej 130 kg, to symbol jego może być wypisany w kolorze czerwonym.
Pracownik od razu zauważy, że należy zamontować element niestandardowy i go nie przeoczy. Możliwe jest również użycie barw do wyodrębnienia elementów zgodnie z ich kategorią. Ponadto, kierownicy produkcji mają możliwość przesyłania na ekrany produkcyjne indywidualnych wiadomości tekstowych przypisanych do konkretnych pozycji zamówienia. Informacje te są przydatne w przypadku nietypowych rozwiązań lub kiedy pozycje wymagają szczególnej uwagi. Tym sposobem nawet najdrobniejsze szczegóły nie zostaną pominięte w procesie produkcji.
Minimalizacja skutków zakłóceń w procesie produkcji
Jednym z głównych powodów zakłóceń w procesie produkcji są braki lub wady materiałów, takie jak uszkodzone profile, pęknięte szyby czy brak elementów okuć. Takie problemy mogą prowadzić do przestojów, pogorszenia jakości produktów, wzrostu kosztów operacyjnych oraz opóźnień w realizacji zamówień. Kluczowym elementem minimalizacji skutków zakłóceń jest szybkie i skuteczne zgłaszanie problemów. Dotychczas, gdy pracownik produkcji zauważył nieprzewidzianą sytuację, miał obowiązek niezwłocznie poinformować przełożonego, aby ten podjął odpowiednie działania.
Wiązało się to jednak z koniecznością opuszczenia własnego stanowiska pracy. Po powrocie pracownik musiał wznowić pracę i kontynuować realizację kolejnych pozycji z planu produkcji. Niezgłoszenie błędu może prowadzić do pogorszenia jakości finalnych produktów, a przerwanie pracy przez pracownika może powodować opóźnienia i zakłócenia w ciągłości produkcji. Dodatkowo, niezgłoszona informacja o błędzie mogłaby też zostać utracona w toku prac, przez co nie byłaby ona efektywnie rozwiązana.
Moduł „Podgląd na produkcji” rozwiązuje te kwestie umożliwiając pracownikom szybkie zgłaszanie problemów. Kierownicy produkcji mogą zdefiniować wiele rodzajów błędów przypisanych indywidualnie do różnych stanowisk pracy. Takimi błędami przykładowo mogą być „pęknięta szyba” lub „porysowany profil”. Zgłoszenie błędu może nastąpić po wybraniu komunikatu błędu z rozwijalnej listy lub zeskanowaniu umieszczonego na tym stanowisku specjalnego kodu kreskowego komunikatu błędu. Następnie pracownik skanuje standardową etykietę produkcyjną. Wtedy komunikaty o błędach są automatycznie przekazywane do programu Stolcad® Professional, a status błędu jest natychmiast widoczny w programie. Kolor wyświetlanej linii zgłoszonego zlecenia zmienia się automatycznie, dzięki czemu wyróżnia się ono na tle zleceń, w których nie wykryto problemów.
Gdy kierownik produkcji zauważy tak podświetlone zlecenie, to może wejść w jego szczegóły. Tam w przypadku zgłoszonego błędu od razu widoczne jest której pozycji on dotyczy. Dodatkowo można zobaczyć jaki to jest błąd, czas jego zgłoszenia, dane osoby zgłaszającej, a także z jakiego stanowiska pochodzi zgłoszenie. Na tej podstawie kierownik może podjąć odpowiednie działania w dogodnym czasie, a po rozwiązaniu problemu może usunąć informację o błędzie bezpośrednio ze stanowiska pracowniczego, skanując przeznaczony do tego specjalny kod kreskowy. Takie rozwiązanie znacząco poprawia stabilność procesu produkcji i minimalizuje straty związane z przestojami. Pracownik nie musi odchodzić od stanowiska, aby poinformować przełożonego o błędzie. Może odłożyć problematyczny wyrób i kontynuować pracę nad kolejną pozycją.
Produkcja bez papieru – oszczędność i zrównoważony rozwój
Moduł „Podgląd na produkcji” eliminuje konieczność drukowania papierowej dokumentacji, wprowadzając cyfrowy przepływ danych w zarządzaniu procesem produkcyjnym. Niezbędne informacje są w czasie rzeczywistym przekazywane na odpowiednie terminale przy stanowiskach pracy, dokładnie wtedy, kiedy są one potrzebne. Przepływ danych jest ograniczony do niezbędnego minimum zwiększając wydajność i bezpieczeństwo produkcji. Cyfrowy przepływ danych to gwarancja, że dane trafią tylko mam gdzie powinny i dokładnie wtedy, kiedy są potrzebne.
Produkcja bez papieru jest nie tylko praktycznym rozwiązaniem, ale również krokiem w kierunku ekologicznej przyszłości. Korzyści płynące z cyfrowej produkcji to nie tylko oszczędność papieru i redukcja kosztów operacyjnych, ale również wzmocnienie pozytywnego wizerunku firmy, jako organizacji dbającej o środowisko. Firmy, które zdecydują się na tę formę produkcji, wyróżniają się na rynku, przyczyniając się do zrównoważonego rozwoju. Czy dziś można jeszcze sobie pozwolić na pozostawanie przy tradycyjnych procesach opartych na dokumentacji papierowej?
Moduł "Śledzenie produkcji"
Zdalne monitorowanie postępów prac na produkcji w czasie rzeczywistym
Wirtualny obraz całej produkcji bez wychodzenia z biura
Moduł „Śledzenie produkcji” to nowoczesne narzędzie dla kierowników produkcji, umożliwiające monitorowanie i odwzorowanie fizycznego procesu produkcyjnego w czasie rzeczywistym. Cały przebieg produkcji jest rejestrowany i odzwierciedlany w programie komputerowym, co pozwala na śledzenie postępów na każdym etapie – od rozpoczęcia zlecenia po jego finalizację – bez konieczności opuszczania biura. Dane z hali produkcyjnej są automatycznie gromadzone w centralnej bazie programu Stolcad® Professional i wizualizowane w oknie zleceń oraz panelu śledzenia produkcji. Każdy skan kodu kreskowego zostaje zapisany jako indywidualny wpis, przypisany do konkretnej sztuki okna w zleceniu. Dzięki temu rozwiązaniu zyskuje się pełną kontrolę nad procesem produkcji, zwiększając efektywność zarządzania.
Rejestrowane informacje obejmują m.in.:
- Statusy przyjęcia wyrobu na stanowisko produkcyjne
- Datę i precyzyjny czas przyjęcia wyrobu na stanowisko
- Osobę przyjmującą wyrób na stanowisko
- Zgłoszenia błędów na produkcji
- Numer zamówienia i nazwę odbiorcy
- Numer pozycji i numer sztuki wyrobu w zamówieniu
- Lokalizację wyrobu na wózku i półce w magazynie wyrobów gotowych
- Przyjęcia i wydania wyrobów do i z magazynu
- Inne informacje zależne od posiadanych modułów i ustawień
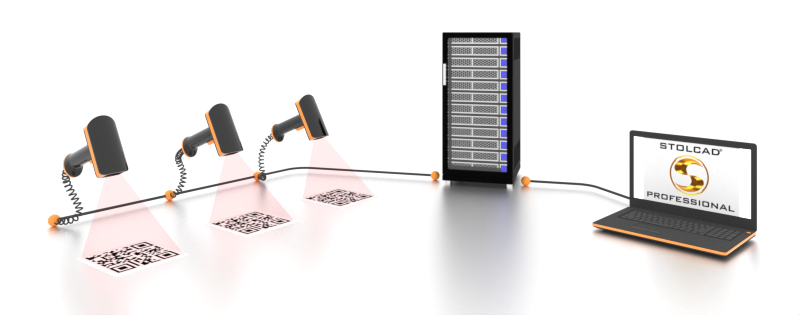
Stan postępu całej produkcji na jednym ekranie
Szczegółowe dane na temat produkcji podsumowywane są na ekranie zleceń programu Stolcad® Professional, gdzie za pomocą pasków postępu i automatycznych statusów obrazowany jest postęp produkcji w odniesieniu do poszczególnych zleceń. Paski postępu mogą być przypisane do konkretnych stanowisk produkcyjnych i będą one w ten sposób informować o ilości pozycji z całości zlecenia, które przeszły już przez te stanowiska.
Przykładowymi kluczowymi stanowiskami mogą być kontrola jakości lub magazyn wyrobów gotowych. Ten sposób wizualizacji pomaga kierownikom produkcji w uchwyceniu bardzo dużej ilości danych i intuicyjnej ocenie w jakim stopniu poszczególne zlecenia zostały zrealizowane. Wszystkie dane szczegółowe, jako cenne źródło informacji do dalszych analiz, mogą zostać wyeksportowane w formie tabelarycznej do programów zewnętrznych.
Moduł "Magazyn wyrobów gotowych"
Kontrola nad stanem magazynu wyrobów gotowych bez wychodzenia z biura
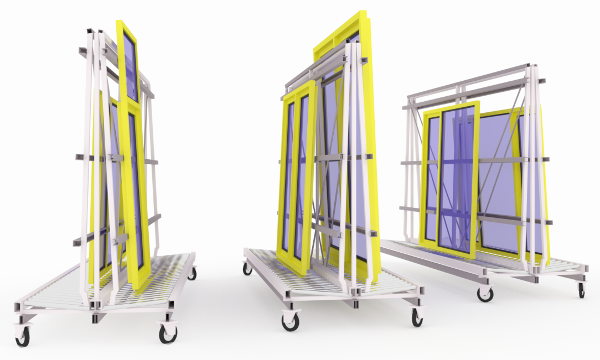
Magazyn wyrobów gotowych to miejsce, w którym na krótki czas przechowywane są gotowe konstrukcje, tuż przed przekazaniem ich do klienta lub przygotowaniem ich do transportu. Bieżące śledzenie informacji na temat stanu magazynu wyrobów gotowych jest kluczowe w kontekście podejmowania decyzji o wydaniu towaru w momencie skompletowania całego zlecenia.
Moduł „Magazyn wyrobów gotowych” pozwala na gromadzenie danych z produkcji oraz ich prezentację w czytelny sposób, tak aby wspomagać podejmowanie decyzji w zakresie przygotowywania zleceń do wydania klientowi. Dane na temat stanu magazynu wyrobów gotowych gromadzone są w programie i możliwe do sprawdzenia bez konieczności wychodzenia z biura.
Wprowadzanie wyrobów do magazynu
Dotarcie gotowego wyrobu do magazynu oraz jego wydanie to dwa kluczowe etapy w procesie produkcji. Aby precyzyjnie odwzorować stan magazynowy w systemie, pracownik magazynu skanuje kod kreskowy konstrukcji przy stanowisku komputerowym odpowiedzialnym za przyjęcie produktu. Przejście wyrobów przez stanowiska magazynowe automatycznie aktualizuje statusy w oknie śledzenia produkcji, zapewniając pełny obraz ich przepływu.
Dodatkowo, jeśli podczas skanowania pracownik wprowadzi numer wózka – na przykład skanując jego kod kreskowy – system przypisze do niego dany wyrób. Możliwe jest również przypisanie numerów przegródek na wózkach, co ułatwia późniejszą lokalizację produktów w magazynie. Przegródki mogą być rejestrowane automatycznie, zgodnie z kolejnością skanowania, lub ręcznie – za pomocą dedykowanych kodów kreskowych.
Okno stanu magazynu wyrobów gotowych
Informacje o wszystkich wyrobach, które zostały przyjęte do magazynu, dostępne są w osobnym zestawieniu tabelarycznym w programie Stolcad® Professional – „Stan magazynu wyrobów gotowych”. Zestawienie te obejmuje dane na temat każdej sztuki wyrobu oraz jej numeru zlecenia, odbiorcy, lokalizacji w magazynie, daty i dokumentu przyjęcia oraz ewentualnie daty i numeru dokumentu wydania.
W oknie stanu możliwe jest dokonywanie korekt, jeżeli informacje na temat lokalizacji na wózku i półce wyrobu nie odpowiadają stanowi rzeczywistemu. Dane ze stanu magazynu wyrobów gotowych możliwe są do wydruku lub wyeksportowania w formie tabelarycznej, na przykład w celach inwentaryzacyjnych.
Łatwe przygotowanie towarów do wydania
Po przejściu wszystkich wyrobów ze zlecenia przez stanowisko przyjęcia do magazynu wyrobów gotowych w oknie zleceń, automatycznie uaktywni się odpowiedni status informujący o gotowości zlecenia do wydania klientowi. Dzięki temu, że informacje o kompletności zleceń są przedstawione na wspólnej tabeli, kierownicy produkcji mogą szybciej podejmować decyzje o ich wydaniu. Kiedy kierownik widzi kompletne zlecenia może rozpocząć procedurę ich wydania, poprzez wygenerowanie nowej listy wydań w Stolcad® Professional. Program automatycznie pomoże zlokalizować potrzebne wyroby podając stosowane informacje na liście wydania.
Warunkiem jest, aby pracownik przyjmujący wyroby do magazynu skanował również numery wózków i ewentualnie przegródek. Podczas procedury pracownik może ponownie zeskanować kolejne wyroby potwierdzając tym samych ich prawidłowe przygotowanie do wydania. Podobnie jak w przypadku przyjęcia, wydanie wszystkich sztuk w zleceniu spowoduje aktywację odpowiedniego statusu w oknie zleceń. Analogicznie jak w przypadku list przyjęć, listy wydań również mogą podlegać procedurze weryfikacji i zatwierdzenia, dając gwarancję, że żaden wyrób nie zostanie nigdy zagubiony. Dzięki temu proces wydania jest szybki i uporządkowany, a wyroby łatwe do odnalezienia.
Rozszerzenia modułu „Zarządzanie produkcją”
Bufor skrzydeł ‒ efektywne łączenie ram i skrzydeł
W produkcji okien zawsze jest stanowisko kompletacji okna, w którym przygotowane wcześniej okute skrzydła są wstawiane do okutej ramy. Ponieważ linia okuwania ram i skrzydeł są to dwie różne linie, kluczowym zadaniem jest synchronizacja dwóch niezależnych procesów – produkcji ram i skrzydeł. Elementy te powstają w różnym tempie i kolejności, co utrudnia ich sprawne łączenie. Pracownik który kompletuje okno ma już do dyspozycji ramę. Teraz musi znaleźć skrzydła do tej ramy. Bez informatycznego wspomagania musi odejść od swojego stanowiska i przeglądając okute skrzydła znaleźć te, które mają być zamontowane w tej ramie. Traci na to czas, a może również zdarzyć się, że takie skrzydła nie są jeszcze gotowe.
Jednym z rozwiązań tego problemu jest bufor skrzydeł, czyli miejsce z ponumerowanymi przegródkami, do którego pracownicy wstawiają gotowe okute skrzydła. W celu optymalizacji tego procesu, pracownik kompletujący okno powinien szybko uzyskać informację, czy są już dane skrzydła gotowe do montażu w przygotowanej ramie i w jakich przegródkach się one znajdują. System bufora skrzydeł umożliwia błyskawiczną identyfikację kompletów – wystarczy zeskanować kod kreskowy na ramie, aby sprawdzić status skrzydeł. Jeśli skrzydła nie są dostępne, pracownik może skanować kolejne ramy. Dzięki temu proces łączenia ram i skrzydeł nie wymaga ścisłej koordynacji między liniami produkcyjnymi, a każda z nich może pracować w swoim tempie, dostosowanym do dostępnych zasobów i planu produkcji.
Pracownik po zakończeniu okuwania skrzydła skanuje na nim etykietę z kodem kreskowym. Na ekranie pojawia mu się numer wolnej przegródki w buforze skrzydeł. Tam ma wstawić okute przez siebie skrzydło. Gotowe skrzydła czekają w buforze, aż wyjmie je pracownik kompletujący okno. Pracownik kompletujący okno skanuje etykietę kodem kreskowym na ramie. Na ekranie wypisują mu się w których przegródkach w buforze skrzydeł znajdują się okute skrzydła do tej ramy. Od razu wie gdzie podejść i skąd wyjąć skrzydła. Po wyjęciu skrzydła zwalnia przegródkę w buforze. Pracownik okuwający skrzydło po jego okuciu i zeskanowaniu etykietki może otrzymać informację, że ma włożyć skrzydło do właśnie zwolnionej przegródki.
Taki cykl powtarza się wielokrotnie. Może zdarzyć się również, że na stanowisku kompletacji zamiast informacji o numerze przegródki gdzie znajduje się skrzydło pojawi się informacja, że takiego skrzydła jeszcze nie ma. Pracownik wtedy chwilowo odstawia daną ramę i bierze następną ramę do okucia. Nie musi już tracić czasu na szukanie nieistniejącego jeszcze okutego skrzydła. W produkcji może działać kilka niezależnych buforów skrzydeł. Oprogramowanie Stolcad® Professional zapewnia precyzyjną synchronizację produkcji i płynną współpracę linii produkcyjnych. Dzięki temu każda linia produkcyjna może działać z maksymalną wydajnością, bez przestojów spowodowanych brakiem komponentów.
Motywacja pracowników poprzez rozliczanie akordowe
Moduł „Akordowe rozliczanie pracowników” rozszerza funkcjonalność modułu „Zarządzanie produkcją”. Zapewnia on efektywne monitorowanie i motywowanie pracowników poprzez przypisywanie punktów akordowych do różnych elementów produkcji. Punkty te, uwzględniające stopień trudności zadań oraz specyfikę stanowisk pracy, są automatycznie rejestrowane i przypisywane do pracowników, co pozwala na obiektywne rozliczenie ich pracy. Moduł umożliwia elastyczne dostosowanie systemu do indywidualnych potrzeb, oferując m.in. mnożniki stanowiskowe oraz opcję tworzenia zespołów roboczych.
Moduł wspiera również obliczanie wynagrodzeń lub premii na podstawie przepracowanych punktów, a podsumowania okresowe pozwalają na analizę wydajności poszczególnych pracowników. Korzyści płynące z rozliczania akordowego obejmują motywację do poprawy wydajności, lepsze wykorzystanie czasu i zasobów oraz wyższą kontrolę kosztów pracy, współmiernych do wyprodukowanych wyrobów. Pracownicy produkcyjni, dzięki sprawiedliwemu systemowi wynagrodzeń, mają możliwość wyższych zarobków, co pozytywnie wpływa na ich zaangażowanie i rozwój zawodowy.
Często zadawane pytania (FAQ)

1. Czy moduł „Zarządzanie produkcją” wymaga stanowiskowych kluczy USB?Nie, do komputerów na hali produkcyjnej nie wpina się stanowiskowych kluczy USB. Moduł w standardzie umożliwia skonfigurowanie dowolnej liczby stanowisk na hali produkcyjnej, bez żadnych ograniczeń.

2. Jak wygląda wdrożenie modułu „Zarządzanie produkcją”?Wdrożenie rozpoczyna się od zdalnego szkolenia i warsztatu, podczas których nasi specjaliści pomagają dostosować system do organizacji pracy Klienta. Następnie program do podglądu produkcji należy zainstalować na hali produkcyjnej na komputerach podłączonych do sieci zakładowej. Komputery te wyposażone muszą być w czytniki kodów kreskowych lub chipów w zależności od wybranej technologii identyfikacji. Konfiguracja Stolcad® Professional oraz narzędzi do monitorowania produkcji jest szczegółowo omawiana w trakcie szkolenia, które najlepiej przeprowadzić na kopii programu Klienta.

3. Kto powinien uczestniczyć w szkoleniu z modułu „Zarządzanie produkcją”? Na szkoleniu z modułu „Zarządzanie produkcją” po stronie Klienta zazwyczaj obecni są kierownicy produkcji, dyrektorzy techniczni lub technolodzy zajmujący się organizacją pracy na produkcji. Osoby te następnie wdrażają zmiany w swojej organizacji. Na szkoleniu nie są i nie powinny być obecne osoby pracujące na linii produkcyjnej. Osoby te bezpośrednio nie powinny decydować w zakresie organizacji produkcji, gdyż takie decyzje powinny podejmować wyłącznie osoby operacyjne.

4. Jak się przygotować do szkolenia z modułu „Zarządzanie produkcją”?Do szkolenia zalecamy, aby przygotować listę stanowisk produkcyjnych w zakładzie, gdyż każde ze stanowisk będzie szczegółowo omawiane i konfigurowane.
***
Jeżeli zainteresował Państwa moduł „Zarządzanie produkcją” to zapraszamy do kontaktu. Nasz zespół z przyjemnością odpowie na Państwa pytania i pomoże dostosować rozwiązanie do Państwa potrzeb.
Wypełnij formularz lub zadzwoń: +48 56 642 66 33
