Companies manufacturing windows, doors, and roller shutters must not only ensure the high quality of their products but also optimize processes, reduce costs, and implement eco-friendly solutions. The Production Management Module supports manufacturers in the digital transformation of production processes. It is a comprehensive IT solution with numerous advantages:
Production Management Module

- Modules
- Production Management Module
Modern production management of windows, doors, and roller shutters
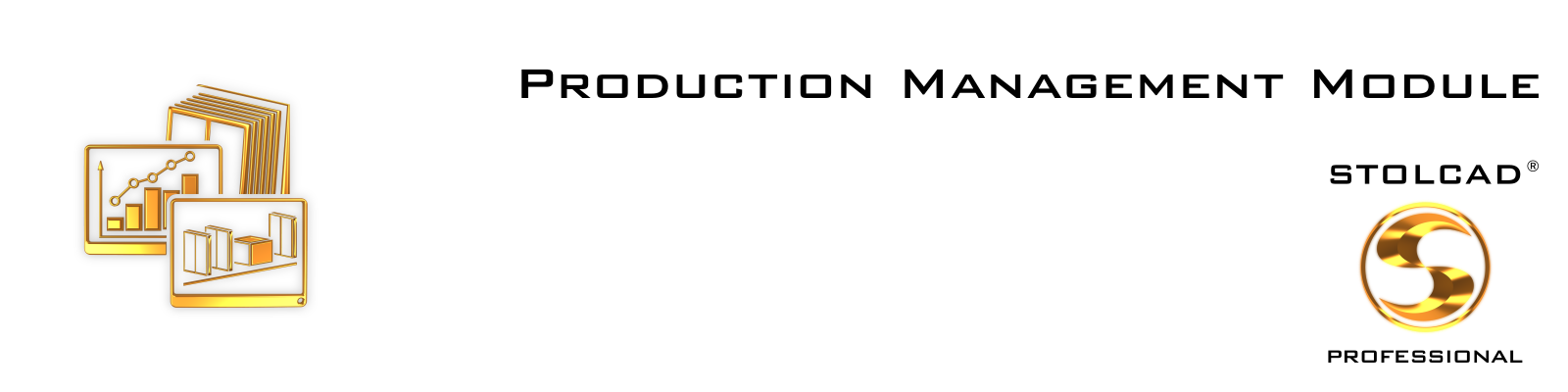
Management and supervision of window, door, and roller shutter production processes
- Remote control of the production process
- Reduction of production costs and better use of resources
- Time savings – shorter production time
- Eco-friendly "paperless" production
- Predictability of the production process
- Improved information flow
- Higher employee productivity
- Fast identification and resolution of production issues
The Production Management Module consists of three integrated IT solutions:
To use the capabilities of the Production Management Module, the implementation of the Production Labels Module is required. The module uses barcode scanning from labels technology, enabling effective tracking and control of production processes.
Production Viewing Module
Displaying assembly lists tailored to individual production stages
The Production Viewing Module is a tool that streamlines manufacturing processes. It uses barcodes placed on production labels attached to profiles. These labels are automatically generated by Stolcad® Professional. Based on the data provided by Stolcad® Professional they can be printed on saws or cutting centres equipped with printers. Alternatively, if these machines do not have printers, labels can be printed in the office.
In that case, they are printed in the same order resulting from the profile cutting optimization. The employee does not have to search for specific labels, as each subsequent cut always matches the next label. An alternative to barcodes on labels is the programming of electronic data into chips placed on profiles. Such a solution is used when traditional labels are problematic, e.g. in wooden technologies.
Computers with barcode or alternatively chip scanners are installed at individual workstations. At subsequent production stages, the data contained in the barcode or chip allow for quick identification of individual elements. This makes it possible to recognize which order and item they come from. Individual construction parts, such as the frame or sash, are also distinguished.
By scanning the code at their workstation, the employee receives a complete set of production information from the database regarding those elements necessary for further work at their station. The computer screen displays the elements to be installed, selected for that workstation, along with a drawing tailored to their needs.
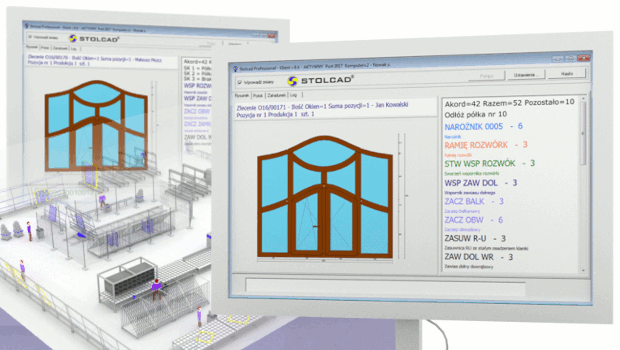
Stories from the production floor – better organization, faster production
Imagine a typical workday on the production floor. An employee approaches their workstation, where a task awaits them as part of the window, door, or roller shutter production stage. Previously, they would have had to search through documentation to find out which elements were necessary to complete the order. Today, a single barcode scan from the production label is enough for a precise list of elements to appear on the monitor. The employee immediately knows what to assemble and what the finished product looks like. No time is wasted, and no mistakes are made. Everything runs smoothly and without delays. This scenario is a reality made possible by the Production Viewing Module.
Reducing chaos and automating key processes not only improve efficiency but also increase work comfort. Employees can focus on their tasks instead of wasting time searching for information. The module allows defining various types of workstations, such as reinforcement, gasket installation, fitting, glazing, or quality control. The module does not impose what these workstations are – the technologist can define them freely. Utilizing the advantages of this solution, production employees receive only the data that are necessary at a given moment. As a result, time is saved that would otherwise be spent on manually organizing documentation and searching for information relevant to a specific workstation.
Effective production starts with individually tailored lists of elements
By scanning a barcode, the employee sees on their monitor which elements of a window, door or roller shutter should be assembled at their workstation, taking into account the specific nature of the tasks performed. The displayed lists of necessary elements for the construction are always tailored to the needs of the specific production workstation. The elements shown on the terminals vary depending on the workstation where the barcode was scanned. The same label scanned at two different workstations will display different information and drawings.
For example, the glazing station will display the glass panes to be installed, while the hardware fitting station will show the necessary fittings for the specific sash. Additionally, the drawing at the glazing station will include glass dimensions, while at the hardware station, it will include sash dimensions. What is displayed is determined by the technologist during system configuration. Such data personalization allows employees to respond quickly and efficiently to production requirements without being overwhelmed by unnecessary information.
With the aid of colour markings for non-standard elements and graphic visualizations of finished products, even the smallest details requiring special attention are immediately noticeable. For instance, at the sash hardware fitting station, the data can be configured so that variable elements such as espagnolette locks are listed in blue, and scissors in green. This way, the employee quickly becomes accustomed to associating the blue-coloured information with the espagnolette to be installed.
Construction drawings can be individually configured for specific workstations. If the structure contains more than one sash, the program will recognize and display information only for the scanned sash, which is particularly important at the hardware fitting station. Such visual assistance ensures precise execution of each production stage, regardless of its complexity. This guarantees that no critical element is overlooked. Employees can quickly respond to specific requirements, improving product quality and shortening order completion time.
Highlighting critical elements and non-standard solutions
Stolcad® Professional also ensures that non-standard and critical elements are never overlooked. Highlighting such elements on the production screen using colours helps employees to identify them. For example, non-standard elements can be marked with bright colours, and a standard corner joint or a sash hinge can be listed in black. At the same time, if a short corner joint or a hinge over 130 kg is to be installed in the sash, its symbol can appear in red so that it is clearly visible.
The employee will immediately notice that a non-standard element must be installed and will not miss it. Colours can also be used to categorize elements. Moreover, production managers have the option to send individual text messages assigned to specific order items directly to production screens. These messages are helpful in the cases of non-standard solutions or when items require special attention. This ensures that even the smallest details are not overlooked during production.
Minimizing the effects of production disruptions
One of the main causes of production disruptions is shortages or defects in materials, such as damaged profiles, cracked glass panes, or missing hardware elements. These problems can lead to downtime, decreased product quality, increased operational costs, and order delays. The key element in minimizing the effects of disruptions is the quick and efficient reporting of issues. Previously, when a production worker noticed an unexpected situation, they were required to immediately inform a supervisor to take appropriate action.
However, this involved leaving someone's own workstation. Upon returning, the worker had to resume work and continue processing the next items from the production plan. Failure to report an error could lead to a decline in the quality of final products, while the absence of the worker from his or her workstation could cause delays and disruptions in production continuity. Additionally, an unreported error might be lost in the workflow and might be not resolved effectively.
The Production Viewing Module addresses these issues by enabling workers to report any problems quickly. Production managers can define various types of errors individually assigned to different workstations. Such errors may include, for example, a "cracked glass pane" or a "scratched profile". A specific error can be reported by selecting the error message from a dropdown list or by scanning a special error message barcode located at the workstation. Then, the worker scans the standard production label. Error messages are automatically sent to Stolcad® Professional and the error status is immediately visible in the system. The colour of the reported order line changes automatically, making it stand out from orders with no detected issues.
When a production manager sees a highlighted order, he or she can check its details. In the case of a reported error, it is immediately clear which item it concerns. Additionally, they can see what the error is, the time it was reported, the data of the reporting person, and the workstation from which the report originated. Based on this, the manager can take appropriate action at a convenient time. After resolving the problem, they can remove the error information directly from the workstation by scanning a special barcode designated for this purpose. This solution significantly improves production process stability and minimizes downtime-related losses. The worker does not have to leave their station to notify a supervisor of an error. They can set aside the problematic product and continue working on the next item.
Paperless production – savings and sustainability
The Production Viewing Module eliminates the need for printing paper documentation by introducing a digital data flow in managing the production process. The essential information is transmitted in real-time to appropriate terminals at workstations exactly when needed. The data flow is limited to the necessary minimum, increasing production efficiency and safety. A digital data flow guarantees that the data reach only where they should and precisely when they are required.
Paperless production is not only a practical solution but also a step towards an eco-friendly future. The benefits of digital production include not only paper savings and reduced operational costs but also strengthening of the positive image of the company as an environmentally responsible organization. The companies that choose this form of production, stand out in the market, contributing to sustainable development. Can anyone today still afford to rely on traditional, paper-based processes?
Production Monitoring Module
Remote real-time monitoring of production progress
A virtual overview of the entire production without leaving the office
The Production Monitoring Module is a modern IT tool for production managers, enabling the monitoring and mapping of the physical production process in real time. The entire production flow is recorded and reflected in the computer program, allowing progress tracking at every stage – from the start of the order to its completion – without having to leave the office. Data from the production floor are automatically collected in the central database of Stolcad® Professional, and they are visualized in the order screen and production tracking panel. Every barcode scan is saved as an individual entry assigned to a specific window piece in the order. With the help of this IT solution, full control over the production process is achieved, increasing management efficiency.
The recorded information includes e.g.:
- Statuses of product receipt at the production workstation
- Date and precise time of product receipt at the workstation
- Person receiving the product at the workstation
- Error reports from production
- Order number and customer name
- Item number and piece number within the order
- Product location on the cart and shelf in the finished goods warehouse
- Receipt and release of products into and from the warehouse
- Other information depending on the available modules and settings
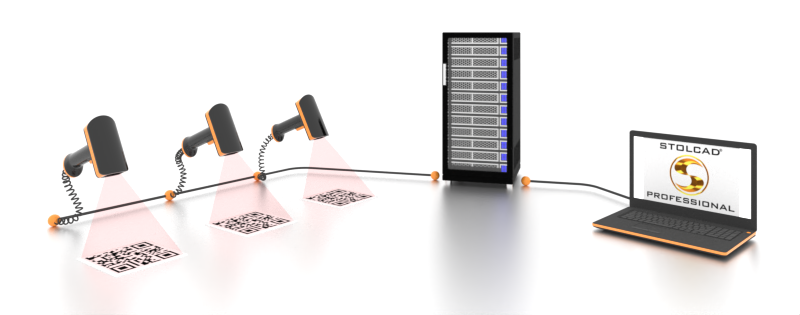
Full production progress displayed on one screen
Detailed production data are summarized on the order screen in Stolcad® Professional, where the production progress of individual orders is visualized using progress bars and automatic statuses. The progress bars can be assigned to specific production workstations, providing information on the number of the items from the entire order that have already passed through these stations.
The example key stations might include the quality control or the finished goods warehouse. This method of visualization helps production managers handle a large amount of data and intuitively assess the completion level of individual orders. All the detailed data, as a valuable source of information for further analysis, can be exported in table format to external programs.
Finished Goods Warehouse Module
Control over the finished goods warehouse without leaving the office
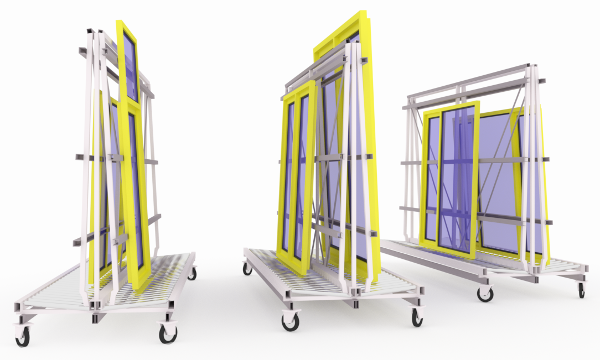
The finished goods warehouse is the place where completed structures are temporarily stored before being handed over to the customer or prepared for transportation. Continuous tracking of the finished goods warehouse status is crucial when deciding to release the goods once the entire order is complete.
The Finished Goods Warehouse Module allows for the collection of production data and their clear presentation to support decision-making in the process of preparing orders for customer delivery. Information on the finished goods warehouse status is collected in the program and can be checked without leaving the office.
Entering products into the warehouse
The arrival of the finished product at the warehouse and its release are the two key stages in the production process. To accurately reflect the warehouse stock in the system, the warehouse worker scans the product's barcode at the computer station responsible for receiving the product. The passage of products through warehouse stations automatically updates statuses in the production monitoring window, providing a complete picture of their flow.
Additionally, if the worker enters the cart number while scanning – for example, by scanning its barcode – the system assigns the product to that cart. It is also possible to assign compartment numbers on the carts, which later helps locate products in the warehouse. Compartments can be registered automatically according to the scanning sequence or manually using dedicated barcodes.
Window of status of finished goods warehouse
Information about all the products received into the warehouse is available in Stolcad® Professional in a dedicated table: "Status of finished goods warehouse". This table includes data for each piece of product, such as the order number, customer, warehouse location, date and receipt document, and possibly the date and release document number.
If the information about the location of a product on the cart and shelf does not match reality, all the needed corrections can be made in the status window. The data from the status of the finished goods warehouse can be printed or exported in table format, for example, for inventory purposes.
Easy preparation of goods for release
After all the products from an order pass through the finished goods warehouse receipt station, an appropriate status in the order panel is automatically activated. It indicates that the order is ready for customer release. Benefiting from the fact that the order completeness information is presented in a shared table, production managers can make quicker decisions about releases. When a manager sees complete orders, he or she can start the release procedure by generating a new release list in Stolcad® Professional. The program automatically helps locating the necessary products by providing relevant information on the release list.
The condition is that the worker who receives products into the warehouse also scans the cart numbers and, if applicable, the compartment numbers. During the release procedure, the worker can rescan each product to confirm their proper preparation for release. As with receipt, releasing all the items in the order activates the appropriate status in the order window. Similar to receipt lists, release lists can also undergo a verification and approval process, ensuring that no product is ever lost. This makes the release process fast and orderly, with products easy to localize.
Extensions of the Production Management Module
Sash buffer – effective synchronization of frames and sashes
In the window production, there is always a window assembly station where pre-assembled sashes are inserted into the prepared frame. Since the lines of fitting hardware to frames and sashes are two different lines, synchronizing these two independent processes – frame and sash production – is crucial. These elements are produced at different speeds and in different sequences, making their efficient assembly more difficult. The worker who assembles the window already has the frame available. Now, they must find the sashes for that frame. Without IT support, they would need to leave their station and search through the completed sashes to find the ones to be installed in that frame. This wastes time and may also result in the situation where the sashes are not yet ready.
One solution to this problem is the sash buffer, which is an area with numbered compartments where employees place completed, hardware-fitted sashes. To optimize this process, the employee assembling the window should quickly receive information on whether the sashes for the prepared frame are ready for assembly and in which compartments they are located. The sash buffer system allows for instant identification of sets – it is enough to scan the barcode on the frame to check the status of the sashes. If the sashes are not available, the employee can scan the next frame. Enhanced by this, the process of joining frames and sashes does not require strict coordination between production lines, and each line can work at its own pace, adjusted to available resources and the production schedule.
After completing the hardware fitting of a sash, the employee scans its barcode label. On the screen the number of a free compartment in the sash buffer is displayed so that it is clear where the sash should be placed. The completed sashes wait in the buffer until the window assembly worker retrieves them and scans the barcode label on the frame. The screen displays which compartments in the sash buffer contain the sashes for that frame. They immediately know where to go and which sashes to take. After removing a sash, the compartment in the buffer becomes available. The employee fitting hardware on a sash, after completing the work and scanning the label, can receive information indicating that the sash should be placed in the just-freed compartment.
Such a cycle repeats itself many times. It may also happen that instead of receiving the compartment number where the sash is located, the assembly station displays a message that the required sash is not yet available. The employee then temporarily sets aside that frame and takes the next one for assembly. He or she no longer has to waste time looking for a sash that does not exist yet. Multiple independent sash buffers can operate in production. Stolcad® Professional ensures precise production synchronization and smooth cooperation between production lines. With the help of the software each production line can operate at maximum efficiency, without downtime caused by missing components.
Employee motivation through piece work accounting
The Piece Work Pay Module extends the functionality of the Production Management Module. It enables effective monitoring and motivation of employees by assigning piece work points to various production elements. These points, reflecting task difficulty and the specifics of workstations, are automatically recorded and assigned to employees, allowing for an objective evaluation of their work. The module allows for flexible system adaptation to individual needs, offering, among other things, workstation multipliers and the option to create work teams.
The module also supports the calculation of wages or bonuses based on accumulated points. The periodic summaries enable performance analysis of individual employees. The benefits of piece work accounting include increased motivation to improve efficiency, better utilization of time and resources, and greater control over labour costs proportional to the manufactured products. Production employees supported by a fair wage system, have the opportunity to earn higher salaries, which positively influences their engagement and professional development.
Frequently Asked Questions (FAQ)

1. Does the Production Management Module require workstation USB keys?No, workstation USB keys are not required for computers on the production floor. By default, the module allows for the configuration of any number of workstations on the production floor without any limitations.

2. How is the Production Management Module implementated?Implementation begins with remote training and a workshop, during which our specialists help tailor the IT system to the client's work organization. Next, our program for production viewing should be installed on production floor computers connected to the company's network. These computers must be equipped with barcode or chip readers, depending on the chosen identification technology. The configuration of Stolcad® Professional and the production monitoring tools is thoroughly discussed during the training, which is best conducted on a copy of the client's program.

3. Who should participate in the training on the Production Management Module?Production Management Module training is usually attended by production managers, technical directors or technologists responsible for organising work on the production floor. These are the people who later implement the changes within the organisation. Employees working directly on the production line do not take part in the training and should not be involved as the decisions should be exclusively made by operational staff.

4. How to prepare for the training on the Production Management Module?We recommend preparing a list of production workstations at your plant, as each workstation will be discussed and configured in details.
***
If you are interested in the Production Management Module, please feel free to contact us. Our team will gladly answer your questions and help tailor the module to your needs.
Fill in the form or call: +48 56 642 66 33
