Piece work pay settlements, unlike fixed wages, link salaries of production employees to the work they actually perform. This system can be highly beneficial for both employers and employees. Clear remuneration conditions serve as motivation for employees and offer a more favourable payroll structure for employers. They avoid excessive costs during periods of reduced production and can rely on higher productivity when orders increase.
Piece Work Pay Module

- Piece Work Pay Module
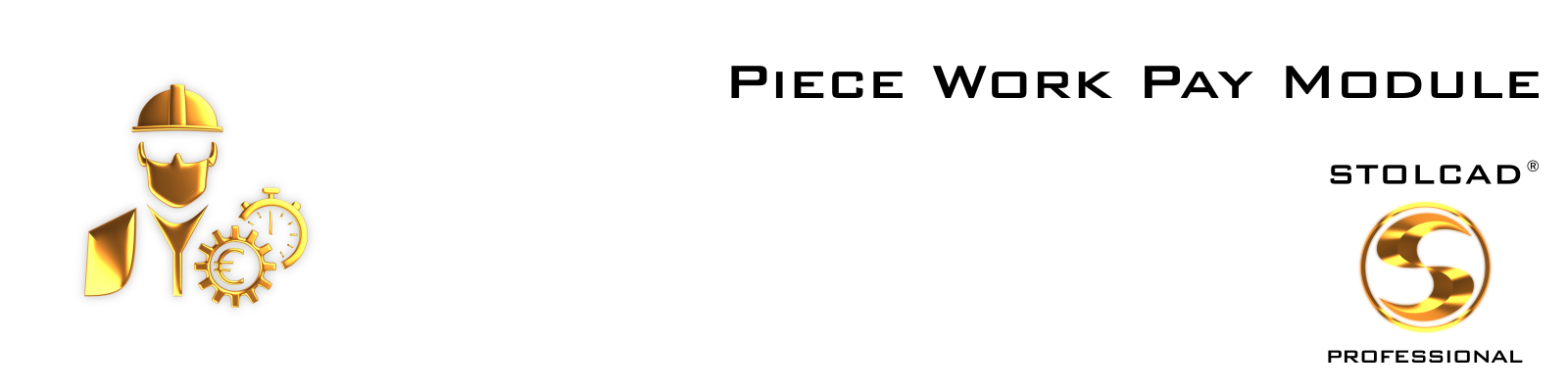
How does the piece work pay system influence motivation and engagement of employees?
The achievable benefits through piece work pay system
- Fair accounting for production employees
- Measurable labour costs proportional to manufactured products
- Greater control over labour costs
- Motivation for production workers to improve their productivity
- Better use of time and resources
- Flexibility in resource management
Adapting the piece work pay system to the complexity of tasks
In order for the piece work pay settlement to function properly, it must be well-designed, considering the quantity, quality and complexity of the work performed. The system should motivate employees to work more efficiently, encourage them to undertake more challenging tasks, reward the most committed workers, and inspire employees to enhance their skills.
The Piece Work Pay Module in Stolcad® Professional, as an extension of the Production Administration Module, supports the design, tracking and modification of the piece work system. A range of module mechanisms allows the system to be fine-tuned based on task difficulty and individual skills of employees.
Automatic recording of tasks performed by employees
To accurately assign tasks to employees, the Piece Work Pay Module uses employee accounts in Stolcad® Professional and their linked accounts in the Production Tracking Module. The module records performed tasks and associates them with the employee currently logged into the software. Employees can log in traditionally by selecting their name from a list and entering a password, or more simply by using a 4-digit PIN, or through scanning an individual barcode on their badge.
Each production activity, along with the associated employee, is transmitted to the main program. The collected data can be reviewed, edited and periodically summarized, and then converted into wages. If certain employees demonstrate above-average quality of work, they may be rewarded with higher rates. For more complex tasks requiring teamwork, groups of employees can be formed and jointly accounted for based on the tasks performed.
Determining complexity of tasks
Wages should reflect the complexity of the work to encourage employees to tackle more challenging tasks and improve their skills. In the Piece Work Pay Module, task difficulty is determined by assigning piece work points to specific components, profiles and accessories, which are displayed at respective workstations.
Piece work points can be individually assigned to elements, profiles, accessories, and panes of glass. If an element passes through a production station, its points are assigned to the worker handling it. The number of points assigned to an element should reflect the complexity of its processing.
Methods of assigning piece work points to elements
There are various methods for assigning piece work points to elements depending on their type. Elements counted per unit, such as locking mechanisms, handles, or hinges, may have a fixed number of points assigned to them. Points for linear elements, such as profiles, gaskets, or glazing beads, can be calculated per unit, for example, in the case of cutting, or per linear meter, as in the case of joining reinforcements with profiles. This method of allocation points enables flexible adaptation of the system to diverse production processes.
The third type of elements, which are glass panes, can be calculated in three ways: per unit, by surface area, or by perimeter (e.g. at the glazing bead station). The level of detail in allocation points can be adjusted as needed, allowing points to be assigned even for the smallest tasks, such as tightening a single screw. A significantly simpler method involves the use of virtual elements, which do not appear on cutting lists but serve solely to allocate piece work points.
Job-related multipliers
Beyond assigning points to elements, the nature of work on different production stations should be considered. The same profile passing through stations like cutting, reinforcement, or fitting involves varying effort and complexity.
This challenge is addressed by applying multipliers of piece work points linked to specific workstations. Each type of station can have an individual coefficient that multiplies the points for elements passing through it and assigns them to the worker, then forwards the total points to the main program.
Periodic summaries
Production data collected in Stolcad® Professional allows the calculation of earnings for individual employees. These calculations can be performed for any selected time frame, with precision to a single day.
The earned piece work points, multiplied by station coefficients and employee rates, are converted into monetary values in local currency. Besides calculating earnings, periodic summaries enable performance evaluation for individual employees.
Benefits of the piece work pay system for production workers
Not only employers but also production workers benefit from piece work pay system. This approach encourages employees who perform their tasks efficiently and quickly to achieve higher earnings. It motivates them to develop skills and enhance productivity, which translates into better performance and work quality. Employees are more willing to take on challenging tasks, knowing that these efforts lead to higher earnings. In contrast, fixed monthly salaries – regardless of the work performed or its level of difficulty – can lead to diminished motivation. Equally important is the satisfaction employees derive from their achievements, along with healthy, mutual competition among colleagues.
- Motivation for efficiency in work – Direct influence on earnings through productivity and engagement.
- Fair compensation – Wages based on work contribution eliminate feelings of unfairness.
- Recognition of effort – More productive workers receive higher pay.
- Transparent rules – Clearly defined allocation of points increases control over work results.
- Equal opportunities – A system based on objective outcomes ensures everyone has a chance to earn more.
- Encouragement for collaboration – Team-based results foster effective cooperation.
Frequently Asked Questions (FAQ)

1. What other Stolcad® Professional modules are required to use the Piece Work Pay Module?In addition to Stolcad® Professional license, it is necessary to have the Production Label Module and the Production Administration Module.

2. What technical equipment is needed to implement piece work pay system in Stolcad® Professional?Technical requirements are similar to the Production Administration Module, including computer workstations with barcode scanners and access to the factory network.

3. How is the implementation of the Piece Work Pay Module for Stolcad® Professional conducted?The module is typically implemented along with Production Administration Module. Implementation involves individual training and online workshops conducted by our experienced specialists. From your side, the process requires the presence of someone responsible for production technology and optionally a network configuration manager. If you already use the Production Administration Module without the Piece Work Pay Module, it can be added under similar conditions. We provide professional support at every stage of the module implementation.
***
If you are interested in the Piece Work Pay Module, feel free to contact us. Our team will gladly answer your questions and help tailor this solution to your needs.
Fill in the form or call: +48 56 642 66 33
