Компании, производящие окна, двери и жалюзи, должны обеспечивать не только высокое качество выпускаемой продукции, но также оптимизировать процессы, снижать затраты и внедрять экологические решения. Модуль «Управление производством» поддерживает производителей в цифровой трансформации производственных процессов. Это комплексное решение с широкими преимуществами:
Модуль «Управление производством»

- Модули
- Управление производством
Современное управление производством окон, дверей и жалюзи
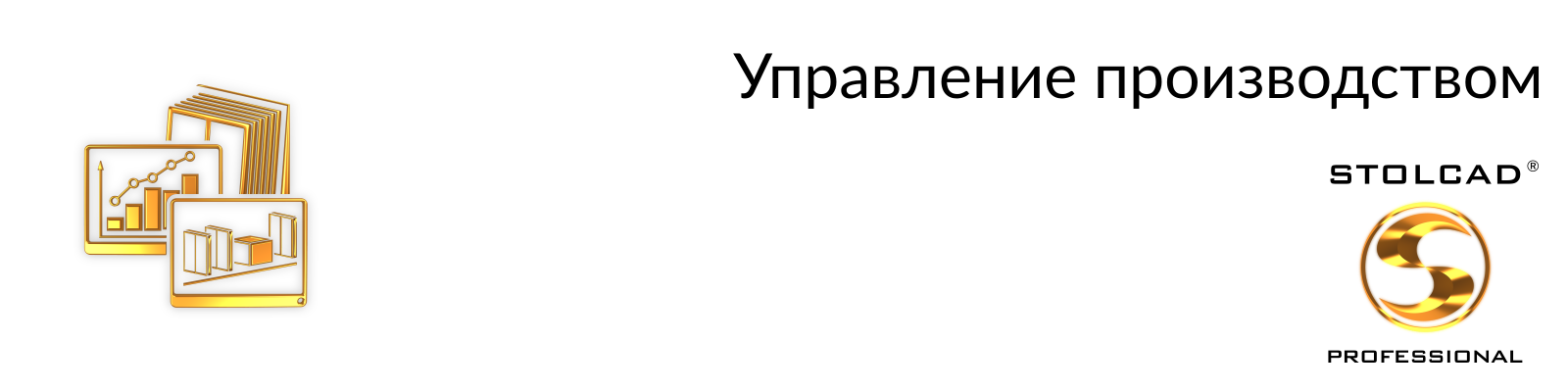
Управление и контроль производственных процессов окон, дверей и жалюзи
- Удалённый контроль производственного процесса
- Снижение производственных затрат и более эффективное использование ресурсов
- Экономия времени — сокращение сроков производства
- Экологичное «безбумажное» производство
- Предсказуемость производственного процесса
- Упрощение потока информации
- Повышение производительности персонала
- Быстрое выявление и решение проблем на производстве
Модуль «Управление производством» состоит из трёх интегрированных IT-решений:
Для использования возможностей модуля «Управление производством» необходимо внедрение модуля «Производственная этикетка». Система использует технологию сканирования штрих-кодов с этикеток, что позволяет эффективно отслеживать и контролировать производственные процессы.
Модуль «Просмотр на производстве»
Отображение монтажных списков, адаптированных к отдельным этапам производства
Модуль «Просмотр на производстве» — это инструмент, позволяющий оптимизировать производственные процессы. Он использует штрих-коды, размещённые на производственных этикетках, наклеенных на профили. Эти этикетки автоматически генерируются программой Stolcad® Professional. Они могут печататься на пилах или резательных центрах, оснащённых принтерами, на основе данных, предоставленных Stolcad® Professional. Если оборудование не имеет встроенных принтеров, этикетки можно распечатать в офисе.
В этом случае они печатаются в том же порядке, который предусмотрен оптимизацией резки профилей. Работнику не нужно искать конкретные этикетки, так как следующее резание всегда соответствует следующей этикетке. Альтернативой штрих-кодам на этикетках является программирование электронного хранения данных в чипах и их размещение на профилях. Такое решение применяется в случаях, когда использование классических этикеток затруднено, например, в деревянных технологиях.
На отдельных рабочих местах установлены компьютеры со сканерами штрих-кодов или, при необходимости, чипов. На последующих этапах производства данные, содержащиеся в штрих-коде или чипе, позволяют быстро идентифицировать отдельные элементы. Благодаря этому можно определить, из какого заказа и позиции они происходят. Также различаются отдельные части конструкции, такие как рама или створка.
Работник, сканируя код на своём рабочем месте, получает из базы данных полный комплект производственной информации по тем элементам, которые необходимы для дальнейшей работы на его участке. На экране компьютера отображаются элементы, которые нужно установить, отобранные для данного рабочего места, а также чертёж, адаптированный под его потребности.
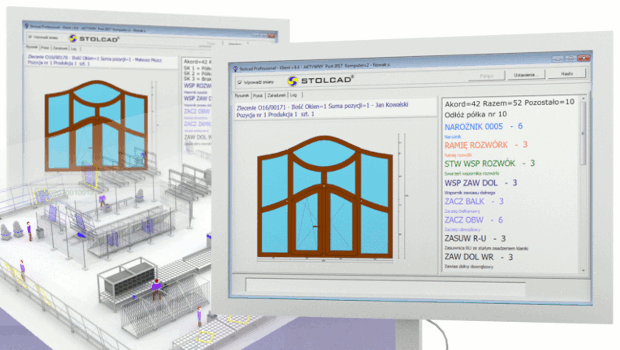
Истории с производственного цеха — лучшая организация, более быстрое производство
Представим себе типичный рабочий день на производственном цехе. Работник подходит к своему рабочему месту, где его ждёт задание в рамках этапа производства окон, дверей или жалюзи. Раньше ему приходилось бы искать документацию, чтобы узнать, какие элементы необходимы для выполнения заказа. Сегодня достаточно одного сканирования штрих-кода на производственной этикетке, чтобы на экране монитора появилась точная информация со списком элементов для выполнения задания. Работник сразу знает, что он должен установить и как выглядит готовое изделие. Он не тратит время, не допускает ошибок. Всё происходит плавно и без простоев. Такой сценарий стал реальностью благодаря модулю «Просмотр на производстве».
Устранение хаоса и автоматизация ключевых процессов не только повышают эффективность, но и увеличивают комфорт работы. Сотрудники могут сосредоточиться на своих задачах вместо того, чтобы тратить время на поиск информации. Модуль позволяет определять различные типы рабочих мест, такие как армирование, установка уплотнителя, фурнитурные работы, остекление или контроль качества. Модуль не задаёт фиксированные типы рабочих мест — технолог может определить их самостоятельно. Благодаря такому решению производственные работники получают только те данные, которые необходимы им в данный момент. В результате экономится время, которое без модуля пришлось бы тратить на ручную организацию документации и поиск информации для конкретного рабочего места.
Эффективное производство начинается с индивидуально адаптированных списков элементов
Работник, сканируя штрих-код, увидит на своём мониторе, какие элементы окна, двери или жалюзи он должен установить на своём рабочем месте с учётом специфики выполняемых задач. Отображаются списки необходимых элементов для выполнения конструкции — всегда адаптированные под потребности конкретного производственного участка. Элементы, показанные на терминалах, различаются в зависимости от рабочего места, где был считан штрих-код. Одна и та же этикетка, отсканированная на двух разных участках, вызовет отображение разных данных и чертежей.
Например, на участке остекления будут показаны стёкла для установки, а на участке фурнитурных работ — фурнитура, необходимая для конкретной створки. Также чертёж на участке остекления будет содержать размеры стёкол, а на участке фурнитурных работ — размеры створок. Что именно отображается, определяет технолог при настройке системы. Такая персонализация данных позволяет сотрудникам быстро и эффективно реагировать на производственные требования, так как они не перегружены ненужной информацией.
Благодаря цветовым отметкам нестандартных элементов и графическим визуализациям готовых изделий даже самые мелкие детали, требующие особого внимания, сразу становятся заметными. Например, на участке фурнитурных работ можно настроить данные так, чтобы переменные элементы, такие как запорные механизмы, выделялись синим цветом, а ножницы — зелёным. Благодаря этому сотрудник быстро привыкает к тому, что информация, выделенная синим цветом, относится к запорному механизму, который необходимо установить.
Чертежи конструкций могут быть индивидуально настроены для отдельных рабочих мест. Если конструкция содержит более одной створки, программа распознает и отобразит данные только о той створке, штрих-код которой был отсканирован, что особенно важно на участке фурнитурных работ. Такая визуальная поддержка обеспечивает точное выполнение каждого этапа производства независимо от его сложности. Благодаря этому ни один важный элемент не будет упущен. Сотрудники могут оперативно реагировать на специфические требования, что повышает качество продукции и сокращает сроки выполнения заказов.
Выделение критических элементов и нестандартных решений
Программа Stolcad® Professional также следит за тем, чтобы нестандартные и критические элементы никогда не были упущены. Выделение элементов на производственном экране с помощью цветов помогает сотрудникам в их идентификации. Нестандартные элементы могут быть отмечены яркими цветами. Например, стандартный угловой соединитель или петля створки могут отображаться чёрным цветом. В то же время, если в конкретной створке должен быть установлен короткий угловой соединитель или петля с нагрузкой свыше 130 кг, то их обозначение может отображаться красным цветом.
Работник сразу заметит, что нужно установить нестандартный элемент, и не пропустит его. Также можно использовать цвета для выделения элементов по их категориям. Кроме того, руководители производства имеют возможность отправлять на производственные экраны индивидуальные текстовые сообщения, связанные с конкретными позициями заказа. Эти данные полезны при нестандартных решениях или когда позиции требуют особого внимания. Таким образом, даже самые мелкие детали не будут упущены в производственном процессе.
Минимизация последствий сбоев в производственном процессе
Одной из главных причин сбоев в производственном процессе являются нехватка или дефекты материалов, такие как повреждённые профили, треснувшие стёкла или отсутствие элементов фурнитуры. Подобные проблемы могут привести к простоям, снижению качества продукции, увеличению операционных затрат и задержкам в выполнении заказов. Ключевым фактором минимизации последствий сбоев является быстрое и эффективное сообщение о проблемах. Ранее, если сотрудник производства замечал непредвиденную ситуацию, он был обязан немедленно уведомить руководителя, чтобы тот принял соответствующие меры.
Однако это требовало покидать рабочее место. После возвращения работнику нужно было возобновить работу и продолжать выполнение следующих позиций по производственному плану. Несообщение об ошибке могло привести к ухудшению качества готовой продукции, а прерывание работы сотрудником — к задержкам и нарушениям непрерывности производства. Дополнительно, несообщённая ошибка могла быть утеряна в ходе работы и не решена вовремя.
Модуль «Просмотр на производстве» решает эти вопросы, позволяя сотрудникам быстро сообщать о проблемах. Руководители производства могут определить множество типов ошибок, привязанных индивидуально к разным рабочим местам. Такими ошибками, например, могут быть «треснувшее стекло» или «поцарапанный профиль». Сообщение об ошибке может быть отправлено путём выбора сообщения из выпадающего списка или сканирования специального штрих-кода ошибки, размещённого на рабочем месте. Затем сотрудник сканирует стандартную производственную этикетку. После этого сообщения об ошибках автоматически передаются в программу Stolcad® Professional, а статус ошибки сразу становится видимым в системе. Цвет строки с заявкой, по которой поступило сообщение, меняется автоматически, благодаря чему она выделяется среди заказов без обнаруженных проблем.
Когда руководитель производства видит такое подсвеченное задание, он может открыть его подробности. В случае зарегистрированной ошибки сразу отображается, какой позиции она касается. Также виден тип ошибки, время её регистрации, данные сотрудника, подавшего сообщение, а также рабочее место, откуда поступило сообщение. На основании этих данных руководитель может принять необходимые меры в удобное время, а после устранения проблемы удалить сообщение об ошибке непосредственно с рабочего места сотрудника, отсканировав специальный штрих-код для этого. Такое решение значительно повышает стабильность производственного процесса и минимизирует потери, связанные с простоями. Сотруднику не нужно покидать рабочее место, чтобы уведомить руководителя об ошибке. Он может отложить проблемный элемент и продолжить работу над следующей позицией.
Производство без бумаги — экономия и устойчивое развитие
Модуль «Просмотр на производстве» устраняет необходимость печати бумажной документации, вводя цифровой поток данных в управление производственным процессом. Необходимая информация в режиме реального времени передаётся на соответствующие терминалы на рабочих местах именно тогда, когда она требуется. Поток данных ограничен до необходимого минимума, что повышает эффективность и безопасность производства. Цифровой поток данных гарантирует, что информация поступит только туда, куда нужно, и ровно в тот момент, когда это необходимо.
Производство без бумаги — это не только практичное решение, но и шаг к экологичному будущему. Преимущества цифрового производства заключаются не только в экономии бумаги и снижении операционных затрат, но и в укреплении позитивного имиджа компании как организации, заботящейся об окружающей среде. Компании, выбравшие такой формат производства, выделяются на рынке, внося вклад в устойчивое развитие. Можно ли сегодня позволить себе оставаться при традиционных процессах с бумажной документацией?
Модуль «Отслеживание производства»
Удалённый мониторинг хода работ на производстве в режиме реального времени
Виртуальное отображение всего производства, не покидая офиса
Модуль «Отслеживание производства» — это современный инструмент для руководителей производства, позволяющий контролировать и воспроизводить физический процесс производства в режиме реального времени. Весь ход производства фиксируется и отображается в компьютерной программе, что позволяет отслеживать прогресс на каждом этапе — от запуска заказа до его завершения — без необходимости покидать офис. Данные с производственного цеха автоматически собираются в центральной базе программы Stolcad® Professional и визуализируются в окне заказов и панели отслеживания производства. Каждый скан штрих-кода сохраняется как отдельная запись, привязанная к конкретному изделию в заказе. Это решение обеспечивает полный контроль над производственным процессом, повышая эффективность управления.
Регистрируемая информация включает, в том числе:
- Статусы приёма изделия на рабочее место
- Дату и точное время приёма изделия на участок
- Сотрудника, принявшего изделие на участок
- Сообщения об ошибках на производстве
- Номер заказа и наименование клиента
- Номер позиции и номер изделия в заказе
- Расположение изделия на тележке и полке в складе готовой продукции
- Приём и выдачу изделий на склад и со склада
- Другую информацию в зависимости от подключённых модулей и настроек
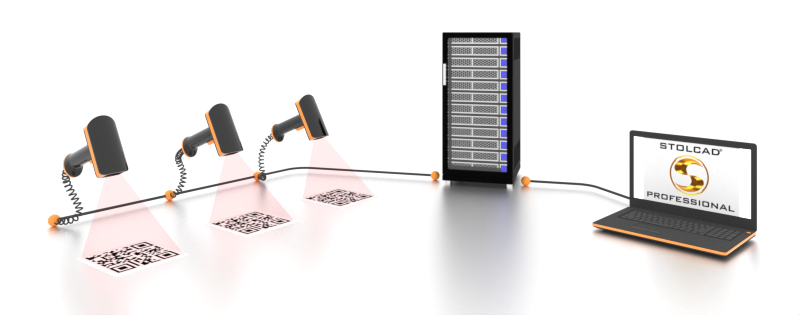
Состояние выполнения всего производства на одном экране
Детальные данные о производстве суммируются в окне заказов программы Stolcad® Professional, где с помощью индикаторов выполнения и автоматических статусов отображается прогресс производства по каждому заказу. Индикаторы выполнения могут быть привязаны к конкретным рабочим участкам, показывая количество позиций из заказа, которые уже прошли эти участки.
Примерами ключевых участков могут быть контроль качества или склад готовой продукции. Такой способ визуализации помогает руководителям производства обрабатывать большой объём данных и интуитивно оценивать степень выполнения заказов. Все детальные данные, как ценная основа для дальнейшего анализа, могут быть экспортированы в табличном виде в сторонние программы.
Модуль «Склад готовой продукции»
Контроль состояния склада готовой продукции, не покидая офиса
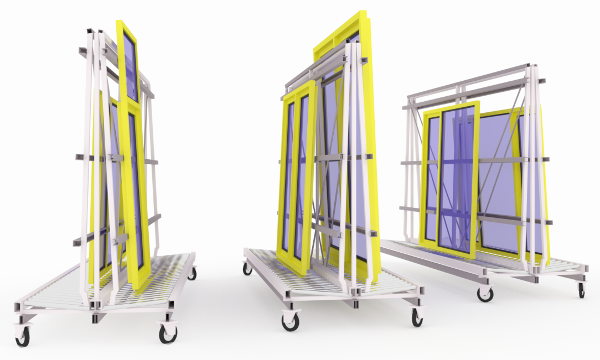
Магазин готовой продукции — это место кратковременного хранения готовых конструкций перед их передачей клиенту или подготовкой к транспортировке. Актуальное отслеживание информации о состоянии склада готовой продукции имеет ключевое значение для принятия решения о выдаче товара в момент комплектации всего заказа.
Модуль «Склад готовой продукции» позволяет собирать данные с производства и отображать их в удобном виде для поддержки принятия решений по подготовке заказов к отгрузке клиенту. Информация о состоянии склада готовой продукции собирается в программе и доступна для проверки без необходимости покидать офис.
Приём изделий на склад
Поступление готового изделия на склад и его выдача — два ключевых этапа производственного процесса. Чтобы точно отразить складские остатки в системе, сотрудник склада сканирует штрих-код конструкции на рабочем месте, ответственном за приём продукции. Прохождение изделий через складские участки автоматически обновляет статусы в окне отслеживания производства, предоставляя полную картину их движения.
Кроме того, если во время сканирования сотрудник укажет номер тележки — например, отсканировав её штрих-код — система привяжет к ней конкретное изделие. Также можно фиксировать номера ячеек на тележках, что упрощает последующий поиск продукции на складе. Ячейки могут регистрироваться автоматически, в порядке сканирования, либо вручную — с помощью специальных штрих-кодов.
Окно состояния склада готовой продукции
Информация обо всех изделиях, принятых на склад, доступна в отдельной таблице программы Stolcad® Professional — «Состояние склада готовой продукции». Эта таблица содержит данные о каждом изделии, включая номер заказа, заказчика, местоположение на складе, дату и документ приёма, а также, при необходимости, дату и номер документа отгрузки.
В окне состояния можно вносить корректировки, если информация о местоположении изделия на тележке или полке не соответствует фактическому положению. Данные из состояния склада готовой продукции могут быть распечатаны или экспортированы в табличном виде, например, для проведения инвентаризации.
Удобная подготовка товаров к выдаче
После прохождения всех изделий из заказа через участок приёма в склад готовой продукции, в окне заказов автоматически активируется статус, информирующий о готовности заказа к отгрузке клиенту. Благодаря тому, что информация о комплектности заказов представлена в общей таблице, руководители производства могут быстрее принимать решения о выдаче. Когда руководитель видит полностью готовые заказы, он может начать процедуру их выдачи, создав новый список отгрузки в Stolcad® Professional. Программа автоматически поможет найти необходимые изделия, указав соответствующую информацию в списке отгрузки.
Обязательным условием является то, чтобы сотрудник, принимающий изделия на склад, также сканировал номера тележек и, при необходимости, ячеек. В процессе выдачи сотрудник может повторно отсканировать изделия, подтверждая тем самым их корректную подготовку к отгрузке. Как и в случае с приёмом, выдача всех изделий из заказа активирует соответствующий статус в окне заказов. Аналогично спискам приёма, списки выдачи также могут проходить процедуру проверки и утверждения, что гарантирует сохранность изделий и исключает их потерю. Благодаря этому процесс выдачи становится быстрым и организованным, а изделия — лёгкими для поиска.
Расширения модуля «Управление производством»
Буфер створок — эффективное соединение рам и створок
В производстве окон всегда есть участок комплектации окна, на котором заранее подготовленные и оснащённые фурнитурой створки вставляются в оснащённую фурнитурой раму. Поскольку линии фурнитурных работ для рам и створок — это две разные линии, ключевой задачей является синхронизация двух независимых процессов — производства рам и створок. Эти элементы изготавливаются с разной скоростью и в разной последовательности, что усложняет их быструю сборку. Работник, выполняющий комплектацию окна, уже имеет в распоряжении раму. Теперь ему нужно найти створки для этой рамы. Без информационной поддержки ему приходится покидать своё рабочее место и вручную искать среди готовых створок те, которые предназначены для этой рамы. Это занимает время, а также может оказаться, что нужные створки ещё не готовы.
Одним из решений этой проблемы является буфер створок — место с пронумерованными ячейками, куда сотрудники помещают готовые створки с фурнитурой. Для оптимизации этого процесса работник, выполняющий сборку окна, должен быстро получить информацию о том, готовы ли необходимые створки для установки в подготовленную раму и в каких ячейках они находятся. Система буфера створок позволяет мгновенно идентифицировать комплекты — достаточно отсканировать штрих-код на раме, чтобы проверить статус створок. Если створки отсутствуют, работник может сканировать следующую раму. Благодаря этому процесс соединения рам и створок не требует жёсткой координации между производственными линиями, каждая из которых может работать в своём ритме, адаптированном к доступным ресурсам и производственному плану.
Сотрудник после завершения установки фурнитуры на створке сканирует этикетку со штрих-кодом. На экране отображается номер свободной ячейки в буфере створок. В эту ячейку он помещает обработанную створку. Готовые створки ожидают в буфере, пока их не заберёт сотрудник, занимающийся комплектацией окна. Работник на комплектации сканирует штрих-код на раме. На экране отображаются номера ячеек в буфере створок, где находятся створки для данной рамы. Он сразу видит, куда подойти и откуда взять створки. После изъятия створки ячейка освобождается. Сотрудник, выполняющий фурнитурные работы, после окончания работы и сканирования этикетки может получить информацию о том, что створку нужно разместить в только что освободившуюся ячейку.
Этот цикл повторяется многократно. Также может случиться так, что на участке комплектации вместо номера ячейки со створкой отобразится сообщение, что такая створка ещё не готова. Тогда сотрудник временно откладывает эту раму и берёт следующую для комплектации. Ему больше не нужно тратить время на поиски ещё несуществующей створки с фурнитурой. В производстве может использоваться несколько независимых буферов створок. Программное обеспечение Stolcad® Professional обеспечивает точную синхронизацию производства и плавное взаимодействие производственных линий. Благодаря этому каждая производственная линия может работать с максимальной эффективностью без простоев из-за отсутствия компонентов.
Мотивация сотрудников через сдельный учёт
Модуль «Сдельный учёт сотрудников» расширяет функциональность модуля «Управление производством». Он обеспечивает эффективный контроль и мотивацию работников путём начисления сдельных баллов за различные элементы производства. Эти баллы, учитывающие степень сложности задач и специфику рабочих мест, автоматически фиксируются и привязываются к сотрудникам, что позволяет объективно оценивать их работу. Модуль позволяет гибко адаптировать систему к индивидуальным потребностям, предлагая, в том числе, коэффициенты для рабочих мест и возможность создания рабочих групп.
Модуль также поддерживает расчёт заработной платы или премий на основе набранных баллов, а периодические отчёты позволяют анализировать производительность отдельных сотрудников. Преимущества сдельного учёта включают мотивацию к повышению эффективности, лучшее использование времени и ресурсов, а также больший контроль над затратами на труд, соответствующими объёму выпущенной продукции. Производственные сотрудники, благодаря справедливой системе оплаты, получают возможность зарабатывать больше, что положительно влияет на их вовлечённость и профессиональное развитие.
Часто задаваемые вопросы (FAQ)

1. Требует ли модуль «Управление производством» наличия USB-ключей на рабочих местах?Нет, к компьютерам на производственном участке не подключаются USB-ключи для рабочих мест. Модуль по умолчанию позволяет настроить любое количество рабочих мест на производстве без каких-либо ограничений.

2. Как проходит внедрение модуля «Управление производством»?Внедрение начинается с дистанционного обучения и практического семинара, в ходе которых наши специалисты помогают адаптировать систему под организацию работы клиента. Далее программу для просмотра производства необходимо установить на компьютеры в цеху, подключённые к корпоративной сети. Эти компьютеры должны быть оснащены сканерами штрих-кодов или чипов в зависимости от выбранной технологии идентификации. Настройка Stolcad® Professional и инструментов мониторинга производства подробно рассматривается в ходе обучения, которое лучше всего проводить на копии программы клиента.

3. Кто должен участвовать в обучении по модулю «Управление производством»?В обучении по модулю «Управление производством» со стороны клиента обычно участвуют руководители производства, технические директора или технологи, отвечающие за организацию работы на производстве. Именно эти лица впоследствии внедряют изменения в своей организации. На обучении не присутствуют и не должны присутствовать сотрудники, работающие непосредственно на производственной линии, так как они не принимают решения по организации производства. Эти решения должны принимать только ответственные операционные лица.

4. Как подготовиться к обучению по модулю «Управление производством»?К обучению рекомендуется подготовить список производственных рабочих мест на предприятии, так как каждое из них будет детально рассмотрено и настроено.
***
Если вас заинтересовал модуль «Управление производством», приглашаем связаться с нами. Наша команда с удовольствием ответит на ваши вопросы и поможет адаптировать решение под ваши потребности.
Заполните форму или позвоните: +48 56 642 66 33
