The waste warehouse in the production of windows, doors, roller shutters and shutters is a place for storing various wastes such as material remnants, packaging waste and chemicals. It has the key role in managing usable waste generated during the production process. The waste warehouse requires careful planning and organization to ensure proper storage, utilization and disposal of the waste. The benefits of effective waste management are obvious: cost savings, environmental protection and increased production efficiency.
Inventory of Waste Warehouse Module

- Inventory of Waste Warehouse Module
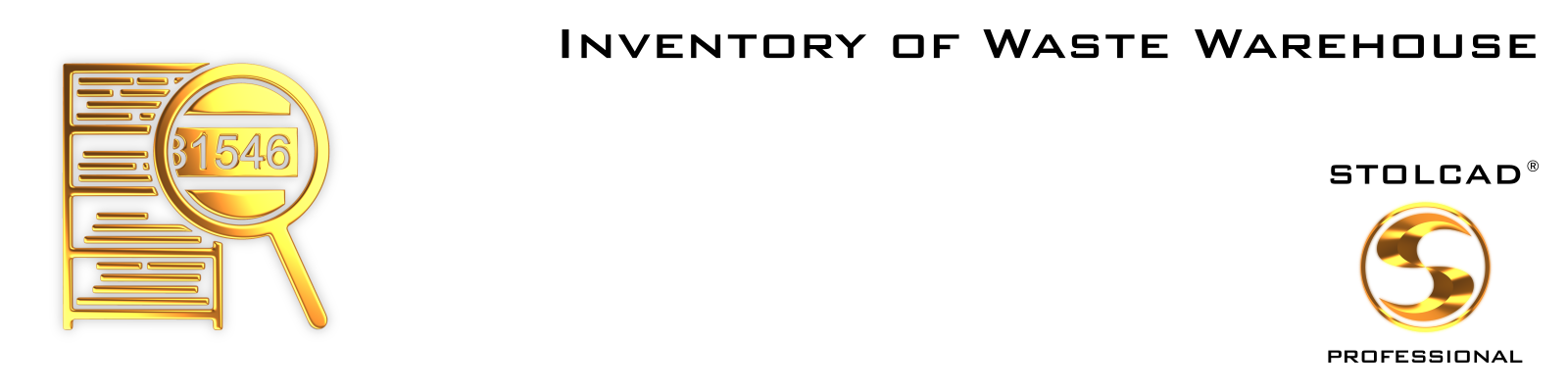
Optimization and management of waste warehouse in Stolcad® Professional
The following description focuses on the biggest challenge, this is effective management of usable waste profiles, which depending on the technology used include pieces of profiles made of PVC, aluminium, steel or wood. The physical state of the waste warehouse must be fully reflected in the virtual waste warehouse in the software that manages the reuse of the waste. In practice, the most important difficulty is to ensure that the state of both warehouses is identical. This problem is solved by our module.
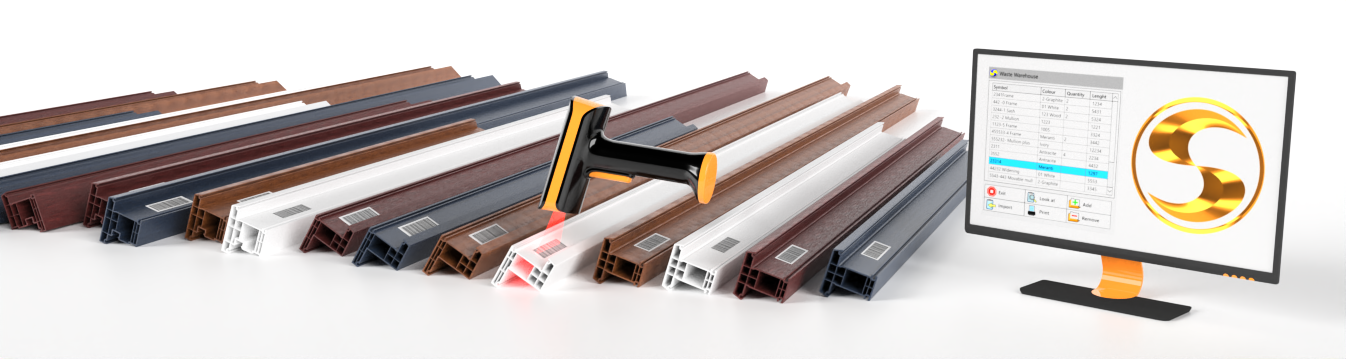
Functions built-in the standard version of Stolcad® Professional
The standard version of Stolcad® Professional has a very efficient built-in function for profile optimization which should be used during current production. The goal of the optimization is to organize the cutting of full profile bars to use as little material as possible while meeting production requirements, considering production organization, work cycles, available machinery, and the assumptions for storing waste profiles in the waste warehouse. The entire process is very comprehensive and consists of many elements that affect production efficiency, which we always discuss and advise our clients during the implementation of Stolcad® Professional.
To put it very simple, Stolcad® Professional during conducting optimization retrieves a list of available profiles from the virtual waste warehouse, and those that meet the criteria for current production are taken from the inventory and used. After making calculations, new waste profile pieces generated during current production are automatically registered and stored in the program. In this way, one profile piece can be reused many times. For example, in the first cycle 1 meter will be used from a 6-meter bar, in the next cycle 1.5 meters will be taken from the remaining 5 meters, and a 3.5-meter piece will be stored again.
Optimization methods for waste management in Stolcad® Professional
The virtual waste warehouse in Stolcad® Professional offers various waste management options tailored to the company's organization, operational structure and available machinery.
The simplest method is the already mentioned classic use of the warehouse: after a single optimization, the program selects profiles from the waste and adds the newly generated usable profiles to the warehouse stock.
Another example method allows configuring data in the program in such a way that for selected profiles or colours a prohibited length range is introduced. For example, all pieces shorter than 20 centimetres can be treated as waste to be discarded, and profiles at least 1 meter long will be stored in the waste warehouse. With this solution, no waste will ever be generated between 20 centimetres and 1 meter on selected profiles or colours. As can be seen, the goal of this approach is to ensure that the waste stored in the waste warehouse can be used in real-life situations. For instance, if a large amount of waste measuring 60, 70 or 80 centimetres accumulated for a window frame, it would be difficult to use it practically, as there are few windows with such dimensions. This would result in an overaccumulation of waste in the warehouse, making it harder to maintain organization and reducing efficiency.
Another solution is when several optimization packages are processed on the cutting centre in one production day. In that case, of course, new usable waste may be generated after each package. For the worker, it would be very inefficient each time to return these pieces to the waste warehouse. Therefore, in such production planning, the next optimization package can first cut from the waste generated in the previous package, even if it means accepting a greater material loss. In this approach, the worker can prepare all the necessary profile bars for the full working day before starting the cutting, and at the end of the work, return to the warehouse only the waste generated in the last optimization package. This planning method is especially recommended in mass, repetitive production, where the work pace is more important than minor material losses.
The Inventory Of Waste Warehouse Module in Stolcad® Professional
In practice, the most important problem to solve related to waste warehouse is ensuring that the waste warehouse state in the computer program matches the actual warehouse state. In the program, everything is calculated perfectly, and each waste is recorded with an accuracy of 1 millimetre. However, in reality, it often happens that a worker, for various reasons, uses the wrong waste profile, or takes a full profile bar instead of the waste element. Sometimes, the waste profile is not placed in the correct location. However, the causes do not always lie with the employee, as he or she may notice a scratch on the profile, the waste profile may be stored for too long, or it may come from a different extrusion batch resulting in a different colour shade. This leads to the situations where instead of theoretically using profiles from the waste warehouse, completely different profiles are used in practice.
The computer program has no knowledge about such situations. Common methods used by companies to solve this problem are organizational approaches. In short, they involve either engaging an additional person for controlling, or imposing additional duties on production workers such as the necessity to record changes and report them to the office for corrections in the virtual waste warehouse. Nevertheless, from our experience, these approaches work well in very few companies. The main reason is the same - human factor that causes discrepancies between the data in the computer system and the actual state of the waste warehouse. An additional difficulty with the manual oversight approach is frequent employee turnover, further complicating the maintenance of up-to-date data in the system. New employees also need time to familiarize themselves with the procedures.
Quick and effective inventory of the waste warehouse
In Stolcad® Professional, we developed a new method that eliminates the inconveniences described above. In the proposed approach, each profile piece in the waste warehouse has a label with a special barcode generated by our software. The worker scans these codes with a scanner (e.g. wireless scanner) connected to a computer, where each scan is recorded as a separate line in a text file, opened for example in notepad. After finishing scanning, the file is saved and imported into Stolcad® Professional with the use of the dedicated module. The advantage of this solution is the ability to conduct quick inventories by scanning selected profiles in the actual warehouse and to automatically update the collected data in the virtual waste warehouse in the program.
In the solution proposed by us, there is no obligation to scan all the profiles in the waste warehouse at once. Inventory can be conducted repeatedly, in small steps, e.g. by scanning all frames and sashes in the basic colour. Such an inventory is conducted quickly - within a few minutes. Additionally, the worker does not need to focus special attention or remember complex numbers, as all the necessary data is contained in the barcode. The proposed inventory method is also error-free. As you can see, regardless of the reasons for the differences between the theoretical state of the waste warehouse in the computer and the actual state in the production, the proposed solution allows for aligning them, ensuring identical data in both warehouses.
Supplementary feature of the module: printing labels from the waste warehouse
In addition to the main module feature of the quick inventory of the waste warehouse, it also allows printing waste labels (without production labels). This is useful during the transition phase when profiles in the warehouse do not yet have barcode labels.
The label printing function is also used when labels on profiles in the waste warehouse are damaged or completely missing. The module allows labelling such profiles, ensuring consistency and precision in the warehouse management.
***
If you are interested in the Inventory Of Waste Warehouse Module, please contact us. Upon receiving your message, we will get in touch to discuss the possibilities of using the proposed solution in the context of your production organization and available machinery.
Fill in the form or call: +48 56 642 66 33
